I ROMANI UTILIZZAVANO UN CEMENTO AUTORIPARANTE: LO STUDIO SCIENTIFICO DI BOSTON E’ LA SVOLTA PER EDIFICI PIU’ RESISTENTI E SOSTENIBILI

La studio condotto dai ricercatori dell’istituto tecnologico del Massachusetts individua nell’utilizzo di clasti di calce il motivo della resistenza delle opere di ingegneria civile dell’Antica Roma. E la formula potrebbe aiutare l’edilizia moderna a realizzazare edifici più resistenti e sostenibili.
Lo studio pubblicato sulla rivista scientifica Science Advances e condotto dell’istituto tecnologico del Massachusetts nelle mura dell’antica città di Priverno, nel Basso Lazio, dove le mura dell’antica città hanno saputo resistere per secoli alla sfida del tempo, ha individuato nell’utilizzo di clasti (frammenti) di calce il motivo della resistenza delle opere di ingegneria civile dell’Antica Roma il segreto della longevità delle costruzioni romane e potrebbe rappresentare una svolta nell’edilizia moderna per permettere la realizzazione di edifici più resistenti e sostenibili nel tempo.
La ricerca sulla miscela di ingredienti lavorati a caldo per ottenere il calcestruzzo romano un particolare materiale pozzolanico, una cenere vulcanica descritta come essenziale dagli architetti del tempo, Vitruvio in primis, impiegato per la realizzazione delle imponenti architetture civili e dei monumenti giunti sino ai giorni nostri ha rivelato la presenza di frammenti porosi di calce, che consentirebbero alla malta di “autoripararsi” nel tempo, grazie all’azione dell’acqua.
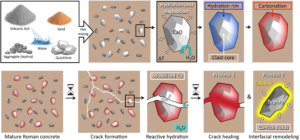
Si è riusciti a determinare, che i romani utilizzavano varie forme di carbonato di calcio, lavorate a temperature molto elevate. E la miscelazione a caldo potrebbe aver contribuito a rendere il prodotto finale ancor più resistente.
La spiegazione tecnica, pur semplificata, è che ad alte temperature i clasti sviluppano un’architettura nanoparticellare fragile, che però si rivela vantaggiosa nell’interazione con l’acqua perché crea una soluzione satura di calcio. Nel contatto con l’acqua, e dunque per esempio con la pioggia cui sono sottoposte tutte le superfici all’aperto, il calcio si cristallizza come carbonato di calcio e ripara le fessure create dalle crepe all’interno del cemento).
La ricerca presenta anche l’applicazione pratica della tesi, riportando i risultati di un esperimento comparato su due campioni di calcestruzzo, uno miscelato a caldo con formulazioni antiche, l’altro realizzato con tecniche moderne, entrambi incrinati meccanicamente in laboratorio, prima di versarvi sopra dell’acqua. Dopo due settimane, il modello antico aveva “riparato” alcune delle sue crepe, mentre il campione moderno risultava ancora incrinato.
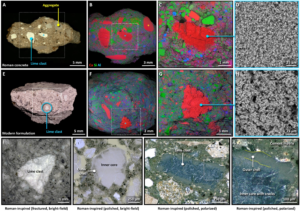
La ricerca sarebbe quindi utile anche a ipotizzare la commercializzazione di una nuova formulazione di calcestruzzo, più resistente e leggero, esemplata sul modello antico, capace di durare più a lungo nel tempo e dunque determinante nel ridurre l’impatto ambientale della produzione di cemento.
In parallelo con gli studi sugli edifici romani, il professore di ingegneria civile e ambientale Admir Masic, formatosi in Italia, all’Università di Torino che ha seguito la ricerca, ha brevettato un cemento “autoriparante”, fondando insieme a Paolo Sabatini la startup DMAT, specializzata nello sviluppo di tecnologie e componenti per creare calcestruzzi durevoli e sostenibili. E dopo anni di test condotti in Svizzera, che hanno portato a ottenere tutte le certificazioni industriali dell’Istituto di Meccanica dei Materiali, il calcestruzzo di nuova generazione (ribattezzato D-Lime) è pronto a entrare sul mercato.
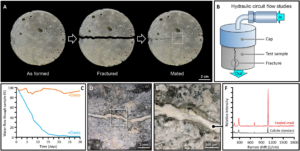
Certificata in Svizzera dall’Istituto di Meccanica dei Materiali, questa nuova generazione di calcestruzzi è caratterizzata dalla capacità appunto di autoripararsi. La tecnologia di Dmat garantisce inoltre un significativo abbattimento dei costi e delle emissioni di CO2 rispetto ai prodotti oggi presenti sul mercato.
Il primo calcestruzzo di nuova generazione ad entrare sul mercato D-Lime combina performance di durabilità e sostenibilità mai raggiunte prima. Questo prodotto permette infatti di allungare la vita e la qualità delle costruzioni attraverso la sua capacità di auto-riparare eventuali crepe. Un processo che, analogamente al cemento romano studiato da Masic, viene attivato dall’acqua che, invece di ammalorare il materiale, richiude le fessurazioni con un processo simile a quello della cicatrizzazione dei tessuti biologici. Il calcestruzzo sviluppato da Dmat consente anche un risparmio del 20% di emissioni di CO2. La realizzazione del calcestruzzo D-Lime è affidata direttamente ai produttori che, tramite un piano di licenze destinato ai produttori, alle aziende di costruzione e agli sviluppatori immobiliari, potranno applicare direttamente la nuova formula senza modifiche agli impianti produttivi. La tecnologia di Dmat permetterà di realizzare prodotti che a parità di performance consentiranno di ottenere un risparmio fino al 50% dei costi.
Le tecnologie di Dmat rispondono alle nuove esigenze di un mercato, quello del calcestruzzo, che oggi vale circa 650 miliardi di euro e che è chiamato a rispondere all’urgente sfida di decarbonizzare i propri processi produttivi, tra i più impattanti del pianeta: la sua filiera industriale è infatti responsabile del 8% delle emissioni di CO2.
“La missione di Dmat è quella di rendere più green e performante un ecosistema dai volumi enormi come quello del calcestruzzo. Per riuscirci, lavoriamo e continueremo a lavorare inseguendo due macro-obiettivi: aumentare la durabilità di questo materiale diminuendone l’impatto ambientale. Oggi siamo l’unico player che riesce a garantire un miglioramento della performance strutturale del 50% con una riduzione delle emissioni di CO2 del 20%. Un risultato straordinario, soprattutto se si considera che permettiamo di raggiungerlo senza costi aggiuntivi, ma, anzi, offrendo il prezzo più competitivo sul mercato” spiega il Ceo di Dmat Paolo Sabatini.
“I volumi di richiesta di calcestruzzo del mercato globale e le finalità per cui viene utilizzato – dall’edificazione di infrastrutture strategiche alla costruzione di alloggi e luoghi di lavoro realizzati in ogni angolo del pianeta con costi contenuti – spiegano da soli quanto esso sia realmente uno dei prodotti più democratici della nostra epoca – continua Sabatini – La cattiva reputazione che talvolta ancora oggi accompagna questo materiale è soprattutto legata ai problemi di durabilità nel tempo e all’impatto ambientale della sua filiera produttiva, in particolare all’utilizzo di uno dei suoi ingredienti principali, il cemento”.
Per accedere allo studio cliccate al seguente link: https://www.science.org/doi/10.1126/sciadv.add1602